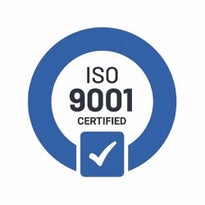
ISO9001:2015
Clause 1: Scope
This clause outlines the purpose of the ISO 9001:2015 standard. It specifies that the standard can be used by any organization, regardless of size or industry, to establish a QMS aimed at consistently meeting customer requirements and enhancing customer satisfaction.
Key points:
- The focus is on meeting both customer requirements and statutory/regulatory obligations.
- It is also applicable to organizations that seek to improve their operations and ensure conformity with established requirements.
Clause 2: Normative References
ISO 9001:2015 refers to ISO 9000:2015 (Quality management systems – Fundamentals and vocabulary) for terms and definitions. This is the only normative reference, meaning it is essential for understanding the terms used in the standard.
Clause 3: Terms and Definitions
This clause refers to the definitions given in ISO 9000:2015. Key terms like “quality,” “risk,” “process,” “interested party,” and “continual improvement” are crucial for understanding and applying the standard.
Clause 4: Context of the Organization
This clause focuses on understanding the organization and its context to develop a QMS suited to its needs and goals.
Key sub-clauses:
- 4.1 Understanding the organization and its context: The organization must determine internal and external issues that are relevant to its strategic direction and affect the QMS.
- 4.2 Understanding the needs and expectations of interested parties: Identify and consider the needs and expectations of stakeholders (e.g., customers, suppliers, regulatory bodies, employees).
- 4.3 Determining the scope of the QMS: Define the boundaries and applicability of the QMS, considering factors like external requirements, the organization’s products/services, and stakeholder needs.
- 4.4 QMS and its processes: Establish and maintain a QMS by identifying processes, inputs/outputs, interactions, and resources required. The organization must also evaluate and improve its processes regularly.
Key focus areas:
- Risk-based thinking is introduced to anticipate potential issues and opportunities.
- Emphasis on aligning the QMS with the organization's strategic direction.
Clause 5: Leadership
This clause highlights the critical role of top management in the effective implementation of the QMS.
Key sub-clauses:
- 5.1 Leadership and commitment: Top management must demonstrate leadership by promoting customer focus, regulatory compliance, and continual improvement of the QMS.
- 5.2 Quality policy: Management must establish and communicate a quality policy that aligns with the organization's strategic goals, customer requirements, and regulatory obligations.
- 5.3 Organizational roles, responsibilities, and authorities: Roles and responsibilities must be clearly defined, with management ensuring that they are understood at all levels within the organization.
Key focus areas:
- Leadership must take accountability for the effectiveness of the QMS and ensure that resources are available.
- Communication of the importance of quality and customer satisfaction is critical.
Clause 6: Planning
This clause focuses on planning the QMS to address risks and opportunities, achieve quality objectives, and ensure the continuous improvement of processes.
Key sub-clauses:
- 6.1 Actions to address risks and opportunities: Organizations must identify risks and opportunities that could affect the QMS and take actions to mitigate risks and exploit opportunities.
- 6.2 Quality objectives and planning to achieve them: The organization must establish measurable and relevant quality objectives aligned with the quality policy. These objectives should drive continual improvement.
- 6.3 Planning of changes: Organizations must plan for changes in the QMS, ensuring changes are carried out in a controlled manner to avoid adverse effects on quality and consistency.
Key focus areas:
- Risk-based thinking is formalized in this section, requiring organizations to proactively manage risks.
- Quality objectives must be specific, measurable, and tied to the organization’s broader goals.
Clause 7: Support
This clause covers the resources needed to implement, maintain, and improve the QMS, including competence, communication, and documented information.
Key sub-clauses:
- 7.1 Resources: The organization must determine and provide the necessary resources (personnel, infrastructure, work environment) for the QMS.
- 7.2 Competence: Ensure that personnel are competent to perform their roles through training, education, and experience. Records of competence must be maintained.
- 7.3 Awareness: Employees must be aware of the quality policy, relevant objectives, and how their work affects the QMS.
- 7.4 Communication: Organizations must establish effective internal and external communication processes, ensuring that relevant information is communicated to stakeholders.
- 7.5 Documented information: Control documentation, procedures, records, and other information relevant to the QMS, ensuring that documentation is available, updated, and secure.
Key focus areas:
- Resource management, including personnel competence and infrastructure, is critical.
- Document control ensures the integrity of the QMS through version control and accessibility.
Clause 8: Operation
This is the most detailed section of ISO 9001:2015, focusing on how the organization plans and controls the processes needed to deliver products and services that meet customer and regulatory requirements.
Key sub-clauses:
- 8.1 Operational planning and control: Organizations must plan, implement, and control production/service delivery processes, including criteria for meeting product requirements and process monitoring.
- 8.2 Requirements for products and services: This includes reviewing customer requirements, establishing contracts, and communicating with customers regarding changes and expectations.
- 8.3 Design and development of products and services: Design and development processes must be planned and controlled to meet customer requirements, with outputs verified and validated.
- 8.4 Control of externally provided processes, products, and services: Organizations must manage suppliers and outsourced processes, ensuring purchased products meet specified requirements.
- 8.5 Production and service provision: Control must be maintained over production and service activities, including validation of special processes, product identification and traceability, and managing customer property.
- 8.6 Release of products and services: Ensure products/services meet customer requirements before they are delivered.
- 8.7 Control of nonconforming outputs: Establish procedures to manage nonconforming products, ensuring they are not inadvertently used or delivered.
Key focus areas:
- Effective planning, control, and monitoring of operational processes are emphasized.
- Product realization processes must be aligned with customer requirements, ensuring conformity and performance.
Clause 9: Performance Evaluation
This clause focuses on how the organization monitors, measures, and analyzes the performance of its QMS.
Key sub-clauses:
- 9.1 Monitoring, measurement, analysis, and evaluation: The organization must define what needs to be measured and how it will be measured, including customer satisfaction and QMS performance.
- 9.2 Internal audit: Regular internal audits must be conducted to evaluate the effectiveness of the QMS and ensure compliance with ISO 9001.
- 9.3 Management review: Top management must review the performance of the QMS at planned intervals, taking into account customer feedback, audit results, and opportunities for improvement.
Key focus areas:
- Data-driven decision-making is promoted through the collection and analysis of performance metrics.
- Internal audits and management reviews are crucial tools for assessing the health of the QMS.
Clause 10: Improvement
This clause focuses on continual improvement to ensure the QMS remains effective and efficient in meeting quality objectives.
Key sub-clauses:
- 10.1 General: The organization must identify opportunities for improvement and implement changes to enhance product quality and customer satisfaction.
- 10.2 Nonconformity and corrective action: Organizations must address nonconformities by taking corrective action to eliminate the root cause and prevent recurrence.
- 10.3 Continual improvement: The organization must make continual improvements to its QMS, focusing on the effectiveness of processes and customer satisfaction.
Key focus areas:
- The standard emphasizes continual improvement as an integral part of the QMS.
- Nonconformities must be managed with a focus on corrective actions and preventing future issues.